The syringe pump offers enormous advantages for microfluidic applications due to its volumetric delivery principle and minimized pulsation. However, it also has a major disadvantage compared to other pumps: the delivery naturally ends as soon as the syringe is empty. This is why the syringe pump is often used in applications where this is irrelevant because the process is paused from time to time and the syringe can be refilled, such as filling individual cavities during pipetting.
In many applications – especially in flow chemistry – an interruption would not be possible, as this would disturb the steady state that has already been set at the beginning of the process by the flow of eluents (chemicals that react with one another).
This problem can be solved by using two syringe pumps per dosing channel, working alternately. This means that when the first syringe is empty, the second syringe takes over the delivery, while a 3/2-way valve refills the first pump from a reservoir. The first syringe then resumes delivery and the second syringe is refilled.
In order not to generate hard impulses when switching the pumps, flatter acceleration and deceleration ramps (crossflow) must be used instead of abrupt stopping when switching from one pump to the other. For applications at higher pressures, however, this is not sufficient to avoid all pressure or flow rate impulses, since the entire mechanical-fluidic system (including the pump that is currently pumping) is pressurized, while the replenished pump – waiting to be used – is under atmospheric pressure. If you now connect this refilled pump to the application by switching the 3/2-way valve, a pressure compensation takes place, which results in a compensation stream. As a result, a certain volume flows from the pressurized application into the unpressurized pump. This reduces the flow rate in the application and, in the worst case, can even become negative for a short time. This must be avoided.
We solve this problem by increasing the pressure of the refilled pump to the same pressure as in the application before connecting it to the application. We achieve this by using two pressure sensors, several valves and an intelligent software implementation. The refilled pump is first run against closed valves and a pressure comparison is made between the two pumps. Based on the parameters defined by the user, the acceptance criterion is reached after a short time, which assumes that the pressure is equal and the valve can therefore be opened for the application.
Since both pressures are the same at the moment of switching on, there is no pressure compensation and therefore no volume compensation flow. The pressure and volume conditions in the application remain constant as desired. The result is a continuous pulsation-free flow (Conti Flow).
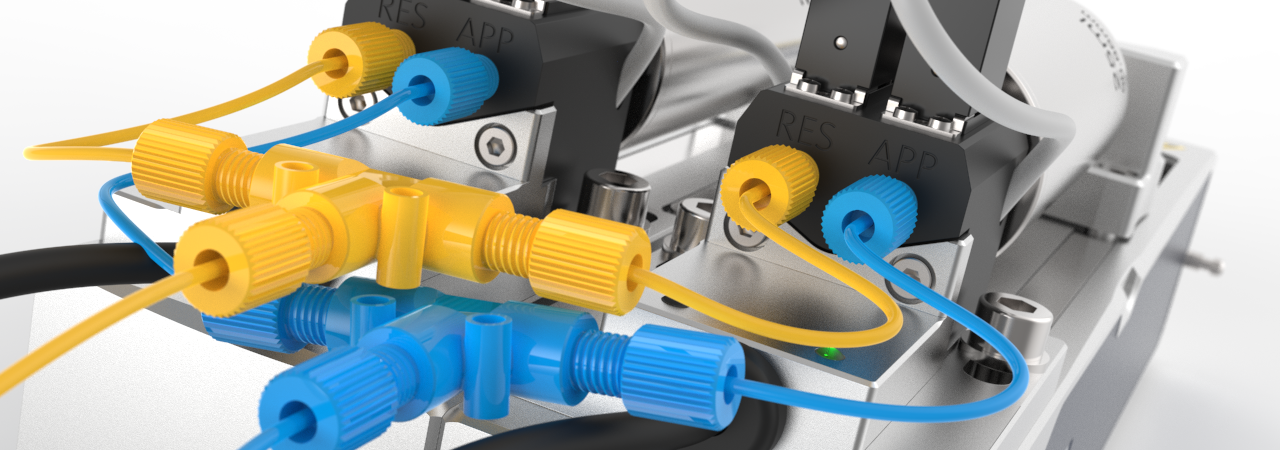
The realization of this process with individual hardware components, such as valves and pressure gauges, could result in a confusing system that is characterized primarily by a jumble of cables and hoses. CETONI not only stands for efficient constructive solutions, we also stand for appealing and innovative design. That is why we have developed an extremely compact module especially for applications with our neMESYS low-pressure and medium-pressure pumps: The Conti-Flow valve. It combines all the described functionalities in the smallest space, replaces a large number of the required hose connections with internal channels, minimizes the dead volume of the application and is also extremely easy to operate thanks to our software. The Conti-Flow unit is suitable for countless substances thanks to the various material combinations from which CETONI customers can choose.