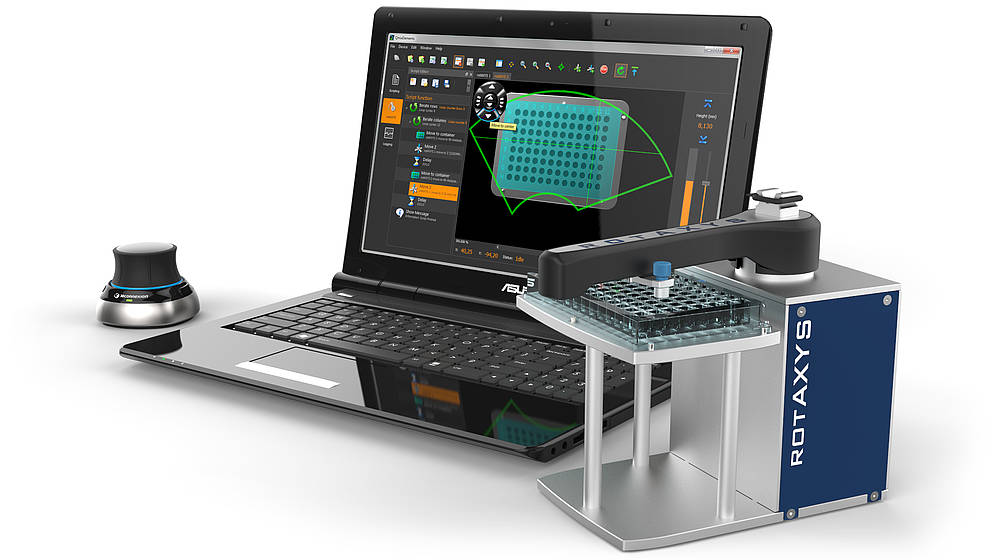
With the positioning system plugins for CETONI Elements, you have full control over your device positioning. The easy-to-use and clearly structured interface makes manual positioning of the systems very easy. Move the systems simply by clicking on a position on the screen or by clicking on a container (well, tank…) on the graphical image.
The current position of the positioning system, the current configuration of your work table, including all containers and microtiter plates, as well as all other important parameters, are displayed in the well structured user interface.
With the powerful script functions, you can easily carry out demanding positioning tasks, using drag & drop. This graphical programming allows you to automate processes and procedures without a lot of training.
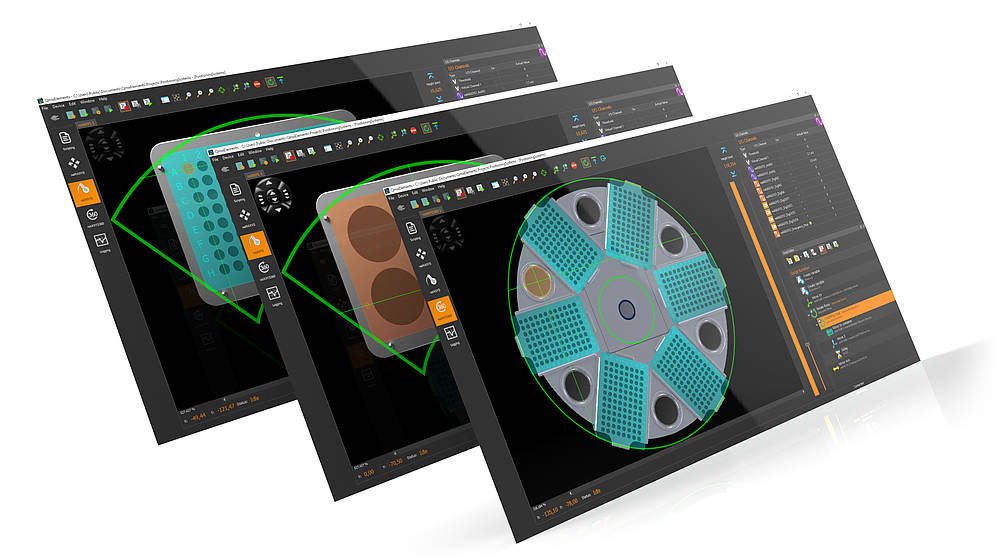
Graphical user interface
Intuitive and easy to use
- Positioning map for convenient XY positioning with a click of the mouse – steplessly zoomable
- easy positioning by clicking on wells, tanks or other containers
- Z panel for positioning the Z axis
- Control pad for manual control of the X, Y and Z axes
- Visualization of all current parameters (positions, status …)
- Fast insertion of the current position in positioning scripts with just one click of the mouse
- All sample containers (corrugated plate, wells, beakers…) are displayed as clickable elements.
- Stepless enlargement using the mouse wheel
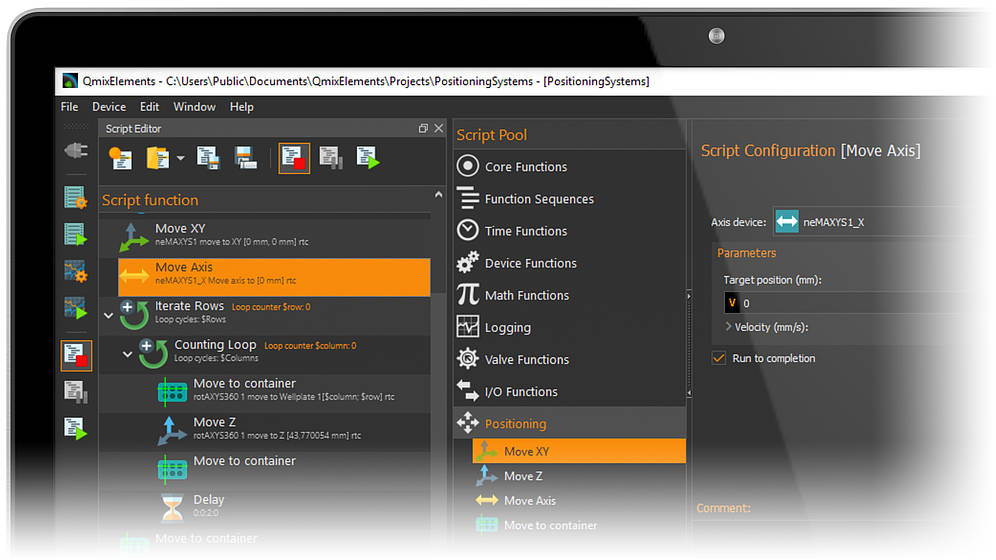
Powerful script functions
Automate via drag and drop
Thanks to integrated script functions, such as Move to XY, Move Z or Move to Container, the positioning systems can be conveniently and easily integrated into the CETONI Elements Scripting System.
With this graphical script programming, you can create complex positioning scripts quickly and easily, using drag & drop. For example, you can scan all wells of a well plate with just 3 script functions.
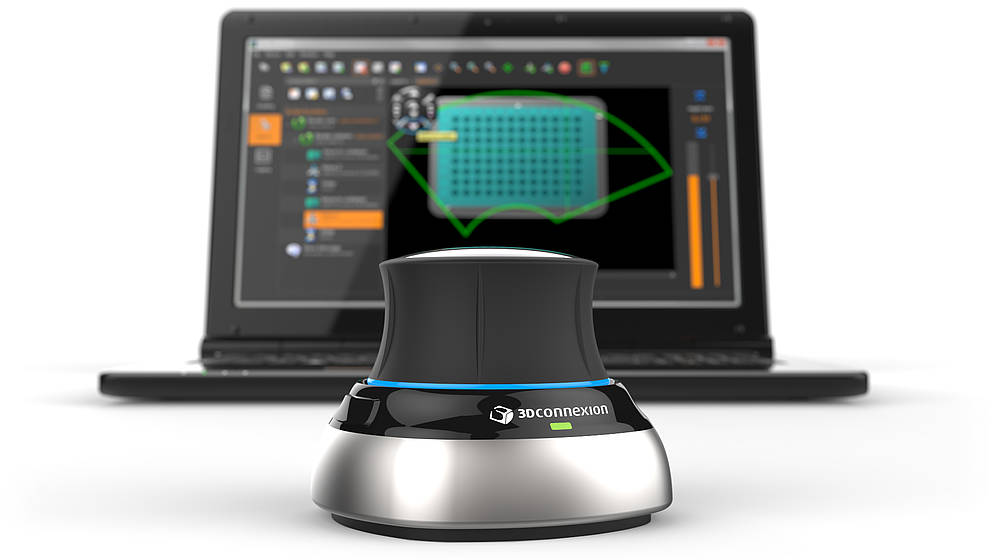
Full 3D mouse support
Intuitive one-hand control
Thanks to the support of the 3D input devices from 3D Connexion (3D mouse), all axes of the devices can be intuitively controlled with one hand. You control the systems as precisely and sensitively as if you were moving the individual axes of the devices directly by hand.