Based on our know-how in the field of automation and your individual process knowledge, we jointly develop a flexible solution that does not limit you, but opens up new possibilities for you and can be quickly adapted. It does not matter to us whether it is a standard method or a batch or flow process. We automate your established manual processes with the help of flexible cobots under the direction of our CETONI Elements software. For this, we use advanced communication standards to control the individual hardware components, including the entire process orchestration. In addition to recording all peripheral process data and user inputs, we also integrate your established analysis technology for the automated generation of measurement data, and make them available for evaluation in a database.
Automation of manual lab processes
The competitive situation requires high research and development speed in many sectors. At the same time, the quality standard increases with the equally careful use of resources. If you are also looking for a solution that relieves you of time-consuming manual processes or standard methods, so that you can invest more of your valuable time in the actual challenges of your profession, then we will find an automation solution for you!
Automation of batch processes
Our portfolio includes state-of-the-art Flow Systems and microfluidic components that enable extensive automation, using innovative microfluidic technologies. In addition, we offer our unique Cobomation approach for all processes that we cannot bring into flow. By this we mean the software managed and robot-based connection of standard methods or batch processes with your existing synthesis and analysis technology. So we use our very flexible automation software CETONI Elements to control all devices in the process.
CETONI Elements – Closing the circle
Our CETONI Elements automation software closes the circle between physical (analog) device technology and digital data processing, i.e. it forms the connection between upstream and downstream processes. In addition to physically linking and controlling all the devices in the process, CETONI Elements also uses advanced technologies such as. DoE (Design of Experiment – statistical test planning), with the help of which the number of tests to be carried out is reduced on the upstream side, and the information obtained can be used immediately for further test planning on the downstream side. This comprehensive approach helps you use your resources effectively in a flexible way, and generate the desired results faster.
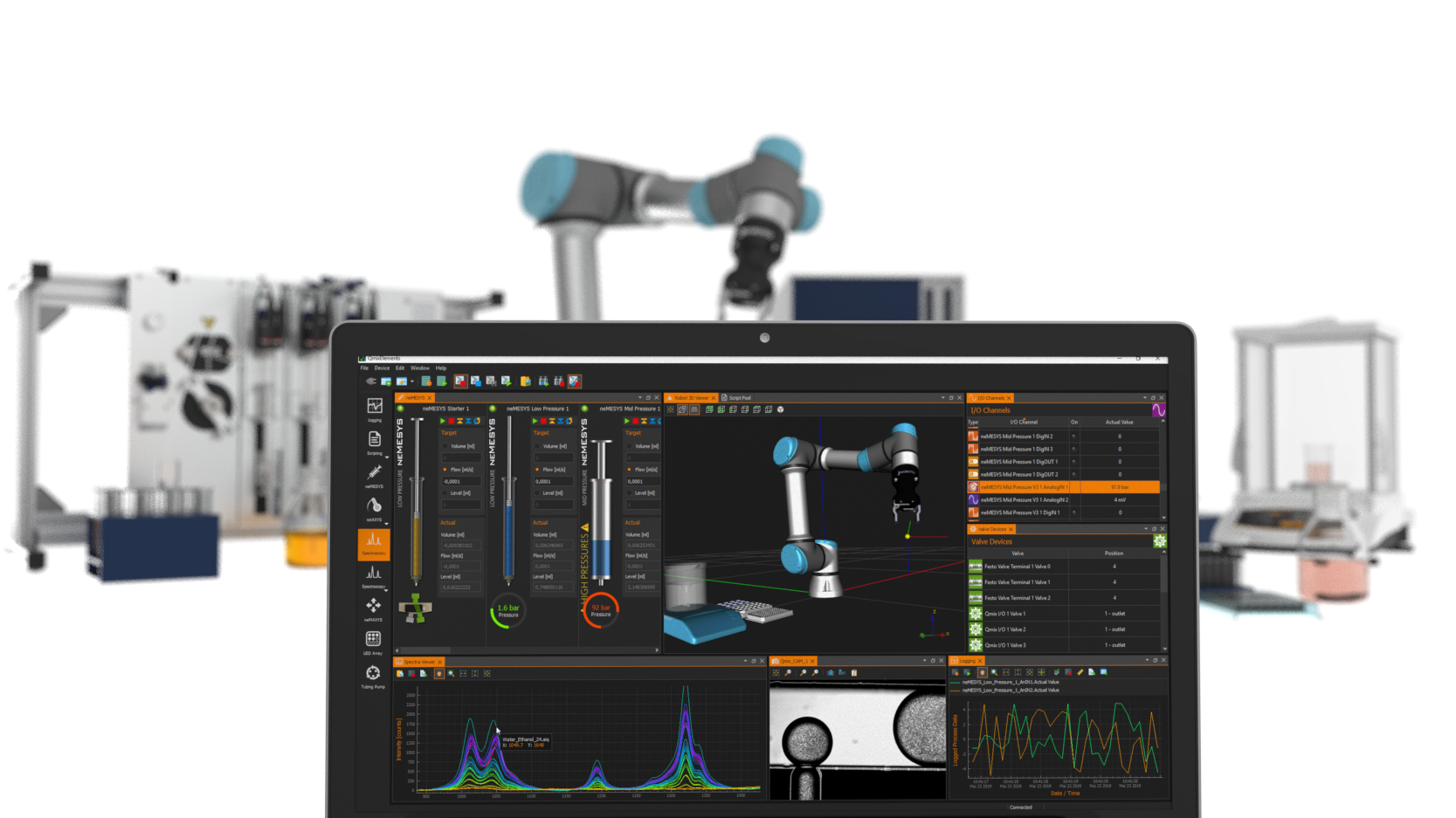
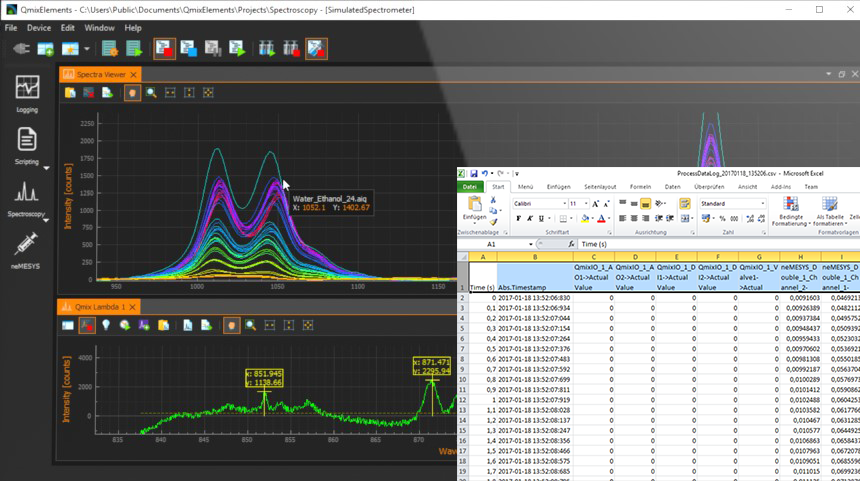
Data Lake and Data Integrity
With this efficient automation approach, the valuable process data is generated reliably and in a resource-saving manner. Then, it is collected in a standardized form in a “data lake” and can therefore be provided in an evaluation-ready format.. You can then access the available data with various tools and methods, in order to further process, analyze and, if necessary, archive it. The importance of data integrity and data security is always part of our thoughts. The secure transmission and making this data available for DoE-software, higher-level laboratory information management systems (LIMS) or artificial intelligence (AI) is just as important to us. With the knowledge gained from externally processed data, new process parameters can be derived and transmitted to our CETONI Elements software for a new analysis run.
Networking of all devices via SiLA (Ethernet)
In our individual and highly flexible solutions, SiLA plays a key role in the fast and individual automation of your process. SiLA stands for standardization in laboratory automation. SiLA’s primary goal is to create an international, open connectivity standard in laboratory automation, through which devices from different manufacturers can communicate with each other in one application.
Your device does not have a SiLA interface?
No problem, we would be happy to check the options for connection via SiLA for you, or simply integrate the device into your automation solution in a different way!
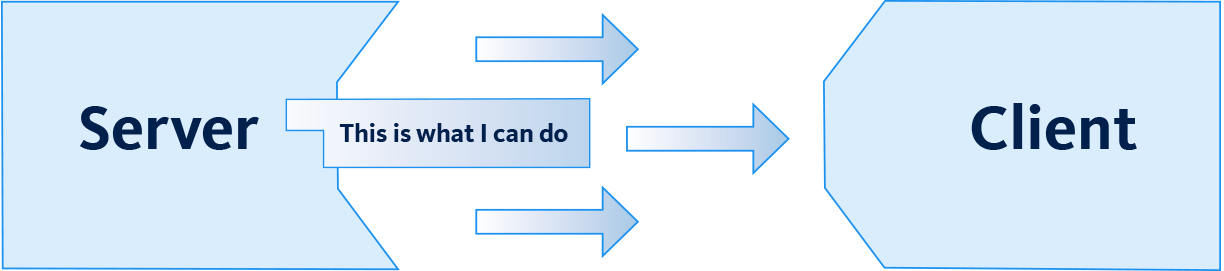
Communication is based on a client-server principle and uses established network standards. The merging of devices from different origins in one application is thus uncomplicated for you as a user, since devices connected to one another with a SiLA interface (i.e. SiLA server), independently provide their functionality (feature) in the network. Now, all that is needed for the logical connection of the functionalities is a manager (in this case called “client”), which conducts the orchestra of devices.
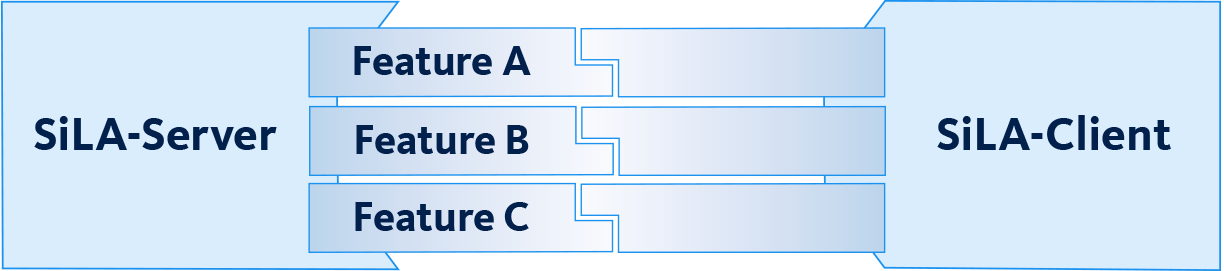
The so-called orchestration of devices in a process, including the collection of data in a database, is done either by our intuitive CETONI Elements software , a superordinate LIMS (laboratory information and management system) or a combination thereof. If you prefer this combination in your laboratory, the setup controlled by CETONI Elements could process the necessary methods as an autarkic automation island, and make (measurement) data available to your LIMS interactively on the downstream side.
Connection to a laboratory information and management system (LIMS)
Our diverse integration options allow you to securely network your process data and research results with your laboratory software, such as laboratory information and management systems (LIMS) or data management systems. For this purpose, we provide you with appropriate documentation for the various programming interfaces (APIs). The diverse interfaces not only allow you to track your sample information, but also to plan, standardize and monitor tasks and workflows, using your laboratory software. This allows you to integrate your liquid handling and automation processes into your workflow and thus increase your productivity and efficiency.
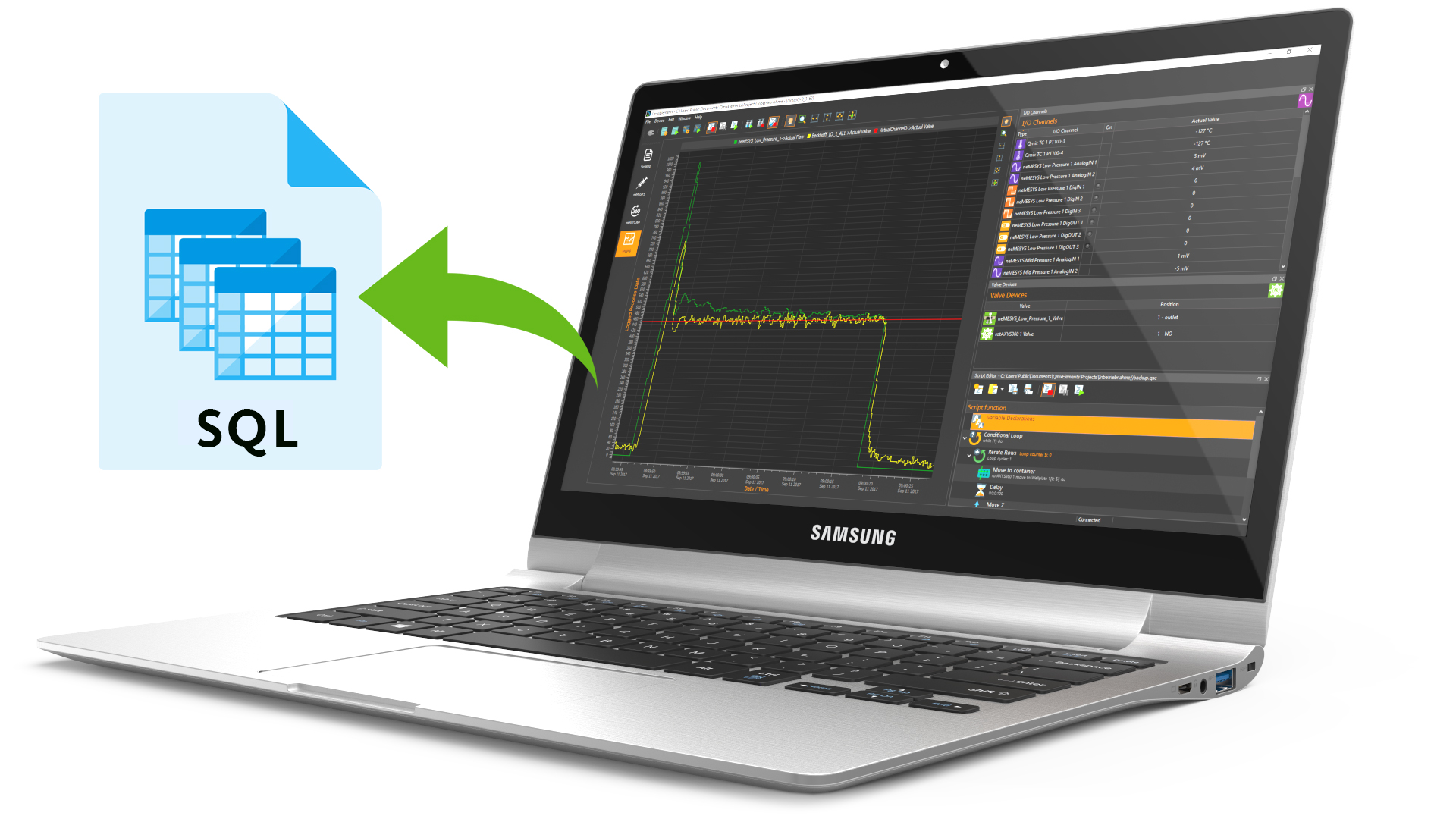
All processes can also be planned and monitored using our CETONI Elements software, into which you can also integrate other devices and signals from your “automation island”. The process data and results are then saved in databases, and are available to other systems. Communication and integration can take place via SiLA , which we have implemented for our CETONI automation solutions.
We support you in the customer-specific integration of our hardware into your LIMS system.
Integration of Design of Experiment (DoE)
Limited material resource and time pressure in the development of processes require advanced methods for test planning. The aim of static test planning or Design of Experiment (DoE) in the laboratory is the reduction of the number of material experiments, in order to generate meaningful results or data. The commonly used experimental procedure of changing individual factors or parameters, step by step, or the trial-and-error principle, bring about the discovery of the global optimum only by chance, while the interaction of influencing factors remains unrecognized. By contrast, statistical test planning is a software-based method for the systematic planning and statistical evaluation of your tests. The functional relationship between influencing and target variables (e.g. pressure, temperature or flow rate) is calculated mathematically with little effort, and the number of experimental tests is significantly reduced. A model is generated in the DoE software and a test plan derived, whereby the relationship between input and target variables can first be specifically described and then examined empirically.
As usual, the physical control of the devices in the process (orchestration) is done by our CETONI Elements software, which we have expanded to include a suitable data interface (for reading * .csv files), to transfer the parameter settings for a planned test run from your DoE software. This seamless transition lets you plan processes efficiently and helps you quickly gain important insights.
Integrating your measuring equipment into the automation system
Our goal is to work with you to automate your application, from sample application to analysis, so that you can gain new knowledge from your experiments more quickly, in order to efficiently optimize processes, synthesize compounds or research interactions. If possible, we integrate your existing analytics systems, such as spectrometers, probes, measuring equipment or other analyzers, into our CETONI Elements software for the automation of a workflow, via familiar software and hardware interfaces.
On one hand, it is possible to visualize simple measuring equipment that supplies analog or digital measurement signals (such as pressure, temperature or pH value) with the help of our I/O module in CETONI Elements, and thus make it usable for you in the process. If devices in the application have a SiLA interface, we use it for communication with your measuring device via CETONI Elements. If integration via SiLA is not possible or the implementation of the interface is too complex, we can use additional software tools to remotely control your device, which frees you as the user from operating it.
Why use a cobot (collaborative robot)?
The term cobot comes from the combination of the English words collaboration and robot and describes robots that have been designed for direct and safe interaction/collaboration with humans. In the collaborative mode, the laboratory staff can do their work in the direct vicinity of the robot and even intervene in the process. In addition, a cobot can be used 24/7 to provide very reliable support to laboratory staff, while ensuring higher throughput with high flexibility at the same time. As part of Cobomation we use cobots to automate time-consuming manual steps in your process, such as liquid handling tasks for sample preparation and post-processing, or manipulation or workflow-supporting transfer tasks. The component that connects everything, and thus your interactive interface to the hardware, is our convenient CETONI Elements software, with which you can introduce your setup to new tasks in a short time.
Your variable workplace in the laboratory
A collaborative robot (cobot) can be used flexibly and quickly – in contrast to classic automation systems that carry out a permanently programmed task. New tasks and work processes can be done in a short time, by simply teaching and integrating the robot controller in CETONI Elements. This allows the use for different and always new tasks that can be spatially and temporally separated, but also run in parallel in individualized work areas. Each user of the robot can use it to design his own individual solution.
For this purpose, the robot can either be used at a new workstation, or it takes on different tasks at customizable workstations that can be rearranged in a flexible way. Depending on the task, we use different effectors such as universal grippers or even a specially developed high-precision ” mobile dosing unit ” for our robot solutions.
The position of the individual devices in the work area, such as beakers/sample reservoirs, pipette tips but also other laboratory devices, such as scales or reactors, can be fixed or flexibly placed, because cobots can be intuitively guided by hand to a point that they should approach at a later time. Once set up, they are easily controlled via CETONI Elements and a sequence can be programmed using simple scripts. Meanwhile, thanks to the built-in sensors, which register touches immediately and stop the cobot, humans and cobots can also move in a shared workspace and work together on a task.
The right gripper for your application
The robot’s gripper is the most important interface to the application, which is why careful selection is essential here. To determine the optimal gripper for your application, the properties of the task, the workpiece and those of the gripper must be taken into account.
It is our aim to work with you to find the most universal solution possible for your process and the tasks at hand or the geometries to be used, as well as offering maximum flexibility for future tasks. If an individual gripper or the gripper span is not sufficient for the different tasks in an application, either double grippers or quick-change devices can be provided. The change process can also be automated, so you do not have to intervene at this point.
Mobile dosing unit for precise liquid handling
Typical liquid handling tasks in your application, such as sample preparation (preparation of dilution series) or transfer, can be carried out in different ways. In the simplest case, the cobot uses a conventional laboratory pipette in the gripper to transfer liquids. The possibilities in terms of throughput, reliability and precision are limited.
Based on our know-how regarding high-precision syringe pumps, we have therefore developed a mobile dosing unit for unsurpassed dosing results for high-precision dosing tasks or demanding media. The nanoliter-precise handling of liquid media of different viscosities and volumes is hereby possible, which gives you a high degree of flexibility and the efficient handling of raw materials.
What process
would you like to map?
We create new things, we integrate seamlessly, we open the door to new goals.
Do you have questions about our products or are unsure of how to put your idea into practice? Our application specialists look forward to seeing you!
Application & Sales
- +49 (0) 36602 338-80
- application@cetoni.de